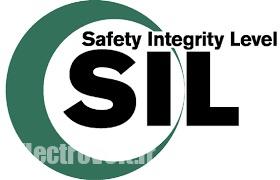
SIL مخفف عبارت Safety Integrity Level به معنای یکپارچگی سطح ایمنی می باشد. گواهینامه SIL یا SIL Certification ارزیابی میزان یکپارچگی سطح ایمنی در سیستم های الکترونیکی می باشد. بر اساس این استاندارد چهار سطح ایمنی تعریف شده است که سطح 4 بیانگر بیشترین میزان کاهش ریسک و سطح 1 بیانگر کمترین میزان کاهش ریسک میباشد. جدول زیر این چهار سطح و میزان ایمنی هر یک را نشان می دهد.
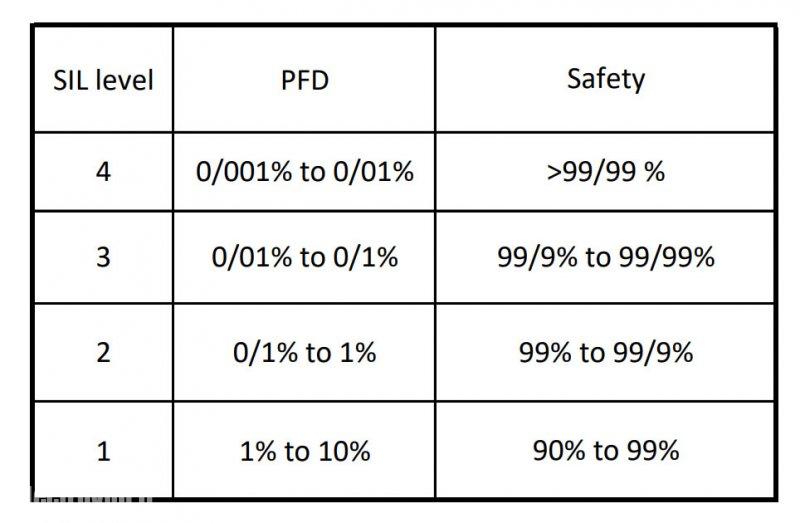
همانطور که در جدول فوق مشاهده می کنید، در سطح 1 میزان ایمنی 90 تا 99 درصد است یعنی میزان شکست سیستم 1 تا 10 درصد می باشد. Fail شدن عملکرد یک تجهیز PFD یا Probability of Failure on Demand به معنای احتمال شکست در لحظه تقاضا می باشد که با ایمنی ( Safety ) رابطه مستقیم دارد. یک ولو ( شیر برقی ) را در نظر بگیرید. فرض کنید از هر ۱۰ بار دستوری که به آن می دهیم یک بار دستور ما Fail شود. PFD این تجهیز ۱ بار در ۱۰ بار یعنی ۱۰% می باشد. هرچه PFD پایین تر باشد احتمال Fail شدن کمتر است. بنابراین هر چه سطح گواهینامه SIL یک تجهیز شماره ی بالاتری داشته باشد آن تجهیز ایمن تر است.
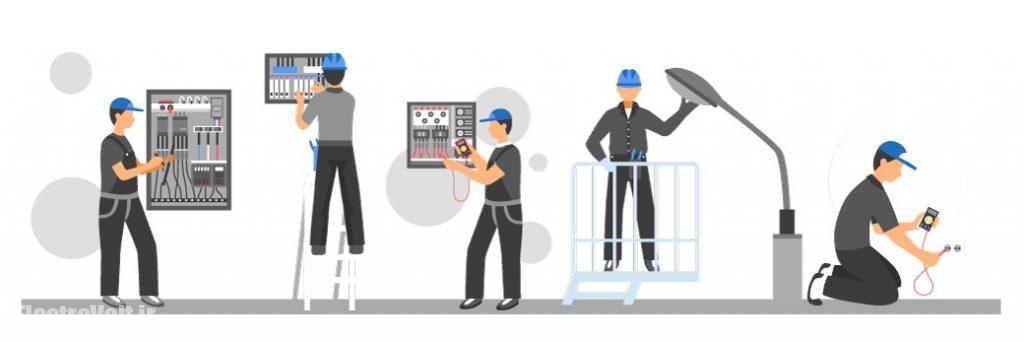
الزام دریافت گواهینامه SIL برای تجهیزات ایمنی در کاربردهای مختلف به صورت زیر تعریف می گردد:
SIL1 کاربرد درجایی است که خسارت به تجهیزات و اموال کوچک می باشد.
SIL2 کاربرد در جایی است که خسارت به تجهیزات و اموال بزرگ بوده و امکان مجروح شدن افراد وجود دارد.
SIL3 کاربرد در جایی است که مجروح شدن افراد و جراحت منجر به فوت وجود دارد.
SIL4 کاربرد در جایی است که امکان فاجعه با مرگ و میر زیاد و صدمات جدی به محیط زیست وجود دارد.
مزیت داشتن SIL بالاتر برای یک تجهیز یکی احتمال خطای کمتر آن و دیگری در دسترس بودن بالاتر عملکرد ایمنی آن تجهیز می باشد. ویژگی مهم SIL این است که بر روی کلیه توابع ایمنی پیاده سازی می شود نه بر روی یک تجهیز خاص. برای مثال یک Transmitter را در نظر بگیرید که SIL3 داشته باشد و درون شبکه ای کار کند که SIL1 باشد. در نتیجه کل شبکه SIL1 خواهد بود و صرف اینکه یک تجهیز دارای SIL3 باشد بهبودی در SIL کل شبکه ایجاد نمی شود.
سیستم دارای تجهیزات ایمن ( SIS ) چیست ؟
سیستم دارای تجهیزات ایمن ( Safety Instrumented System ) که به اختصار به آن SIS گفته می شود، سیستمی است که در آن کنترل مجزا در فرآیندها، در کنار سیستم کنترلی اصلی وجود دارد. برای مثال شکل زیر را در نظر بگیرید که در آن مواد شیمیایی ریخته شده به مخزن توسط شیر ( Valve ) کنترل می شود. باز یا بسته شدن این شیر جریان را به سمت مخزن هدایت می کند. نحوه کنترل مقدار مواد شیمیایی درون مخزن به این صورت است که یک سنسور سطح ( Level Transmitter ) سطح مواد درون مخزن را اندازه گرفته و به عنوان یک ورودی به BPCS مخفف Basic Process Control System نظیر PLC ارسال می شود سپس PLC فرمان های لازم را جهت تنظیم سطح به شیر ارسال می کند.
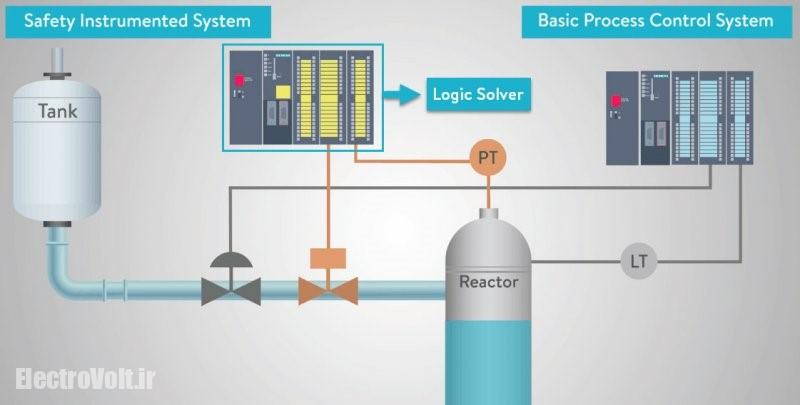
سیستم فوق در شرایط عادی به کار خود ادامه می دهد اما در صورتی که شیر برقی خراب شود چه اتفاقی می افتد ؟ اگر مخزن دارای مواد شیمیایی خطرناک باشد چه خطری جان انسان های اطراف مخزن را تهدید می کند؟
برای افزودن عملکرد ایمنی ( Safety Function ) به سیستم فوق نیاز به مجموعه ی کاملاً مجزای SIS شامل یک سنسورفشار (Pressure Transmitter ) برای سنجش فشار درون مخزن، یک کنترلر یاLogic Solver با سرعت و دسترسی پذیری بالا برای دریافت فشار و ارسال فرمان کنترلی و یک شیر برقی دیگر برای قطع اضطراری جریان و جلوگیری از انفجار یا پارگی مخزن است. حساسیت بالای SIS کمک میکند تا در شرایط خطر مانند یک سیستم قطع اضطراری عمل کند و از بروز فاجعه جلوگیری نماید.
لایه های حفاظتی ( Layer Of Protection )
از یک پروسه توسط لایه های مختلفی محافظت می شود تا در برابر هرگونه رخداد غیر مترقبه مقاوم باشد. به کلیه تمهیدات لازم (اعم از سختافزاری و نرمافزاری) که برای جلوگیری از بروز حوادث یا کاهش ریسک و همچنین ایمنسازی واحد فرآیندی بعد از بروز حادثه اندیشیده میشود، لایه حفاظتی گفته میشود به طوریکه با استقرار این لایهها، فرآیند در حاشیه امن قرار خواهد گرفت. بنابراین LOP در دو دسته اقدامات پیشگیرانه ( Prevention ) و اقدامات کاهشی ( Mitigation ) طبقه بندی می شوند که در شکل زیر مشاهده می کنید:
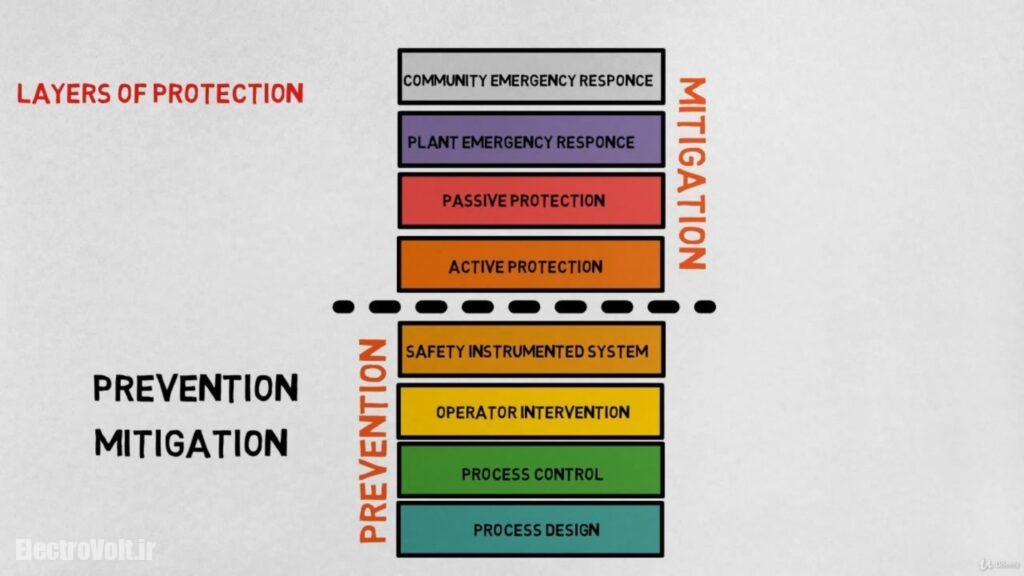
Process Design : برای پیشگیری از هر فاجعه ای اولین لایه محافظتی طراحی پروسه می باشد. پروسه باید طوری طراحی شده باشد که از مهندسین صد در صد محافظت نماید. طراحی پروسه ضعیف موجب تولیدات ضعیف، بهره وری پایین، خطای زیاد، ریسک عملیاتی بالاتر و آسیب به تجهیزات می شود.
Process Control : از آن جایی که هیچ پروسه ای 100 درصد ایمن نمی تواند باشد بنابراین لایه دوم محافظتی کنترل پروسه می باشد. برای این منظور از سیستم های کنترل پروسه BPCS ( مخفف Basic Process Control System ) نظیر PLC ها و DCS ها استفاده می شود که می توانند به صورت دائم از پروسه اصلی فیدبک گرفته و آن را کنترل نمایند.
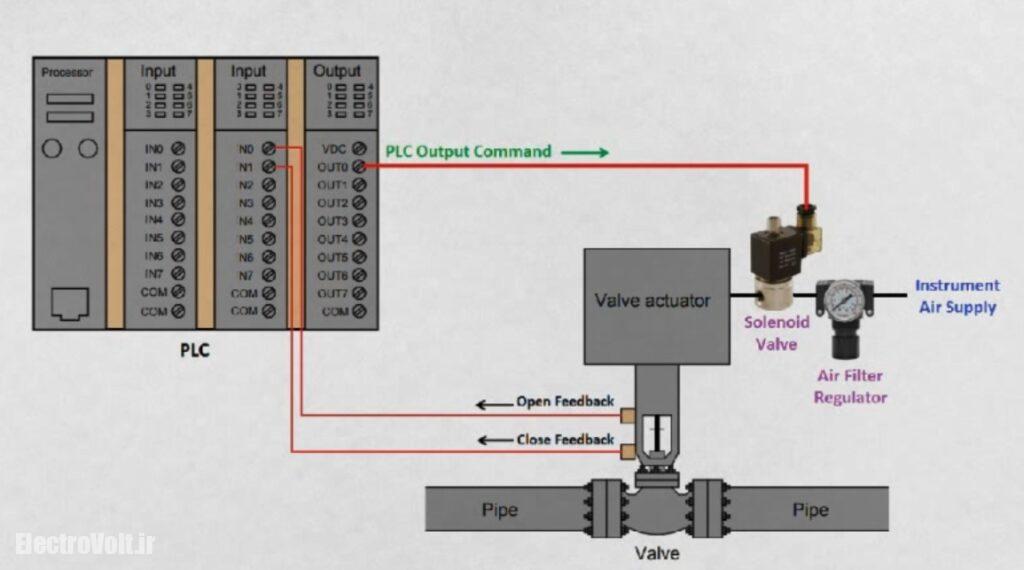
Operator Intervention : لایه سوم محافظتی، محافظت اپراتوری است که توسط کسانی که وظیفه آن ها محافظت از پروسه است صورت می گیرد. این افراد آموزش دیده اند تا در صورت بروز مشکل اقدام لازم را انجام دهند.
Safety Instrumented System : لایه چهارم محافظتی SIS ها می باشند. در صورتی که تمام لایه های قبلی موفق به کنترل پروسه نشوند سپس یک SIS شروع به کار می کند و با توجه به وضعیت اختلال بوجود آمده اقدام از پیش طراحی شده را اجرا می کند تا اینکه سیستم بتواند به سطوح محافظتی قبلی برگردد. در صورت عدم موفقیت این لایه دیگر بحث کاهش خسارت ها مطرح می شود.
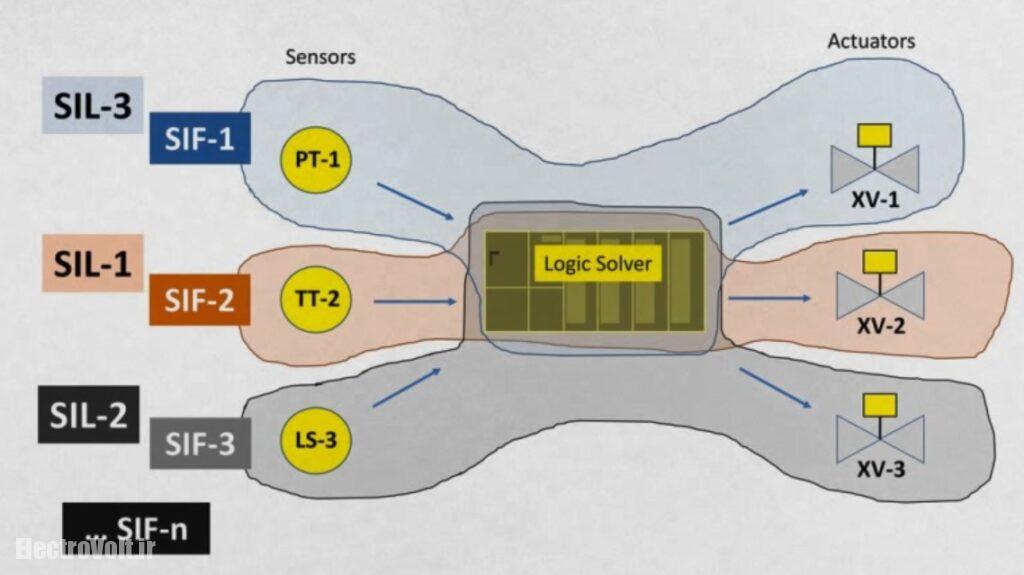
Active Protection : در این لایه محافظتی یک سیستم همیشه فعال قرار می گیرد که در تمام طول پروسه فعال باقی می ماند. برای مثال یک شیر فشار شکن ( Pressure relief valve ) را در نظر بگیرید. در صورتی که فشار درون یک مخزن یا لوله زیاد از حد شود. دیسک کوچکی باز می شود و باعث تخلیه گاز اضافی و پایین آمدن فشار می شود.
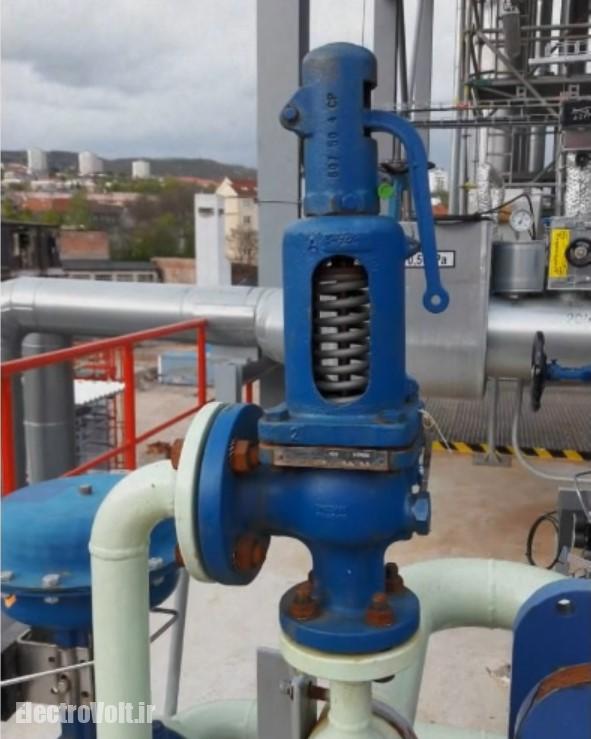
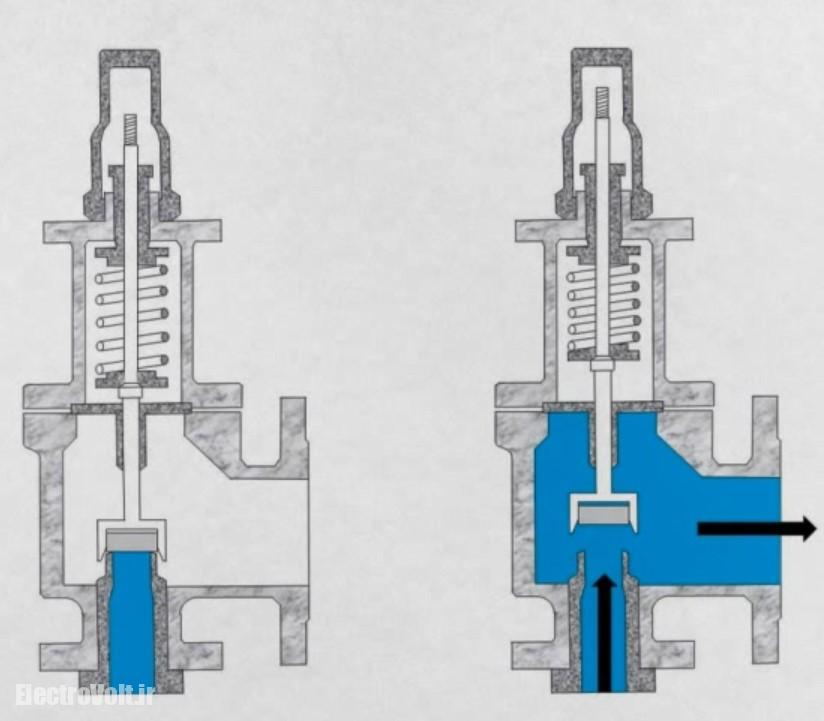
Passive Protection : در این لایه محافظتی یک سیستم ایمنی Standby قرار می گیرد که تنها در مواقع بروز حادثه روشن ( Run ) می شود. برای مثال دیوار زیر را در نظر بگیرید که به منظور جلوگیری از ریختن محتویات مخزن مواد شیمیایی و نفتی روی پرسنل کارخانه استفاده می شود.
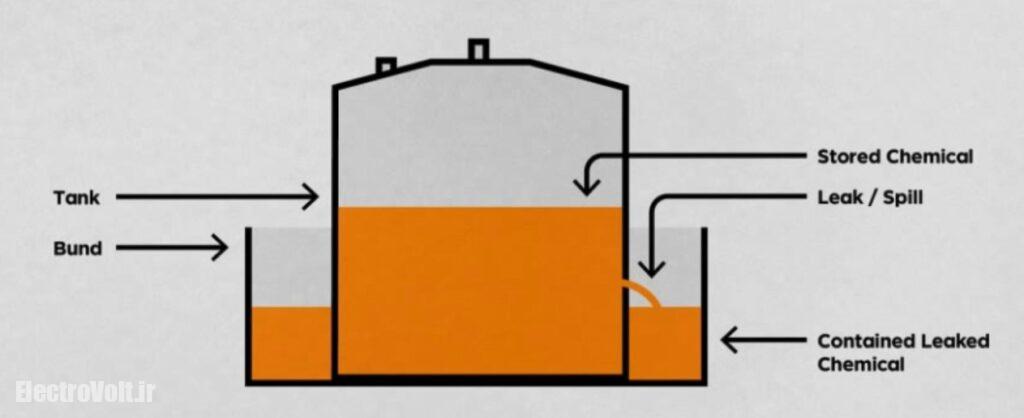
Plant Emergency Responce : در این لایه محافظتی تیم آموزش دیده و همواره آماده پالایشگاه به افراد و تجهیزات پاسخ اضطراری می دهند تا از حریق یا انفجار احتمالی جلوگیری شود.
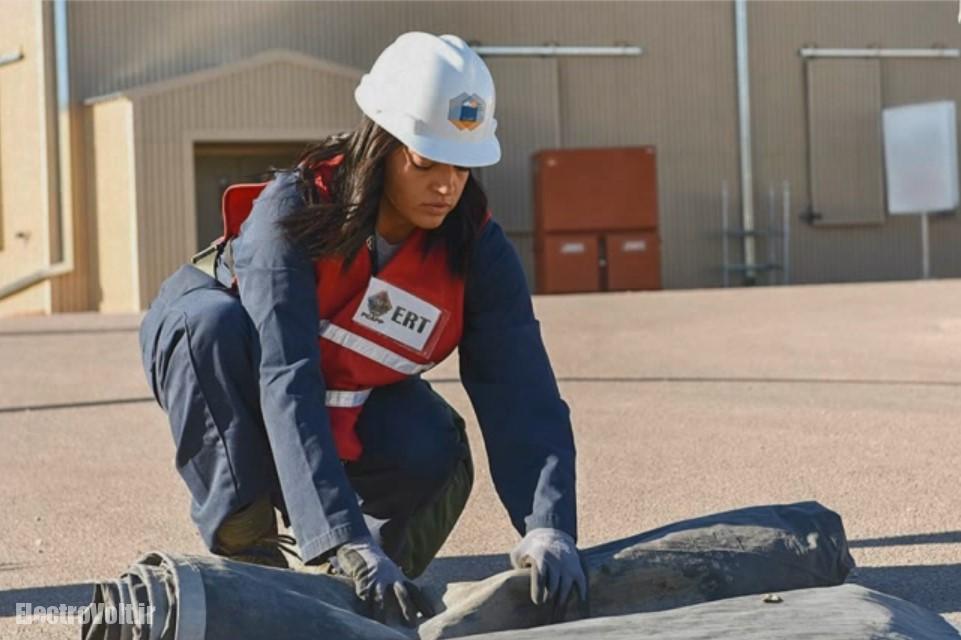
Community Emergency Responce : در این لایه محافظتی آتش نشانی، آمبولانس و دیگر تیم های امدادی خارج از جایگاه به پرسنل و شهروندان در نزدیکی پالایشگاه در صورت بروز حادثه نظیر آتش سوزی و انفجار وارد عمل می شوند.
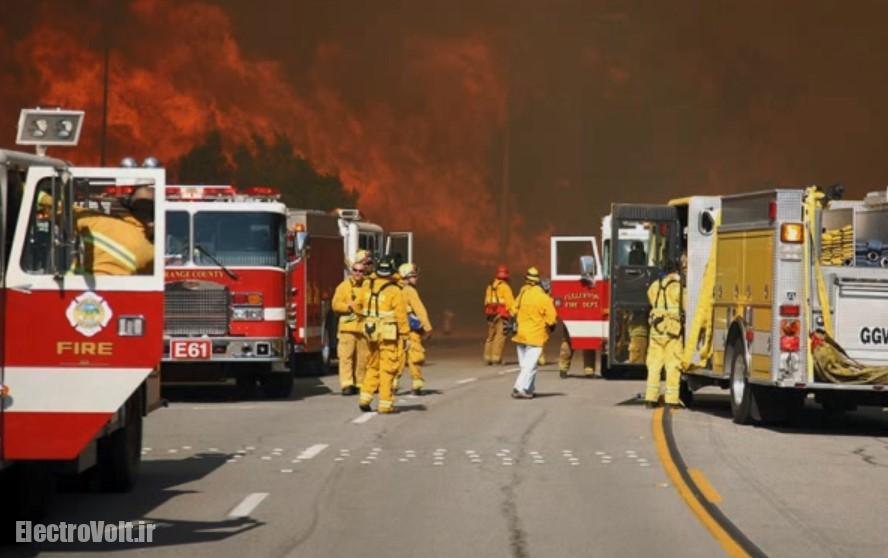
بنابراین جایگاه SIS اهمیت بالایی دارد چرا که می تواند روند پروسه را از حالت خارج از کنترل و بروز خسارت های جانی و مالی به حالت قابل کنترل در آورد.
حالت های مختلف SIS
- STATE OK : یعنی سیستم در حالت IDLE و بدون خطا می باشد.
- STATE SAFE : یعنی SIS در حال اجرای عملکرد ایمنی به منظور دور کردن خطر است، تقاضا ها پاسخ داده می شود و پروسه تحت کنترل است.
- STATE DANGEROUS : در حالتی که SIS نمی تواند تقاضا ها را پاسخ دهد و عملکرد ایمنی نمیتواند به درستی اجرا شود.
- STATE INTERMEDIATE : حالتی که با وجود یک یا چند خطای درونی SIS میتواند تقاضا ها را تا حد امکان پاسخ دهد.
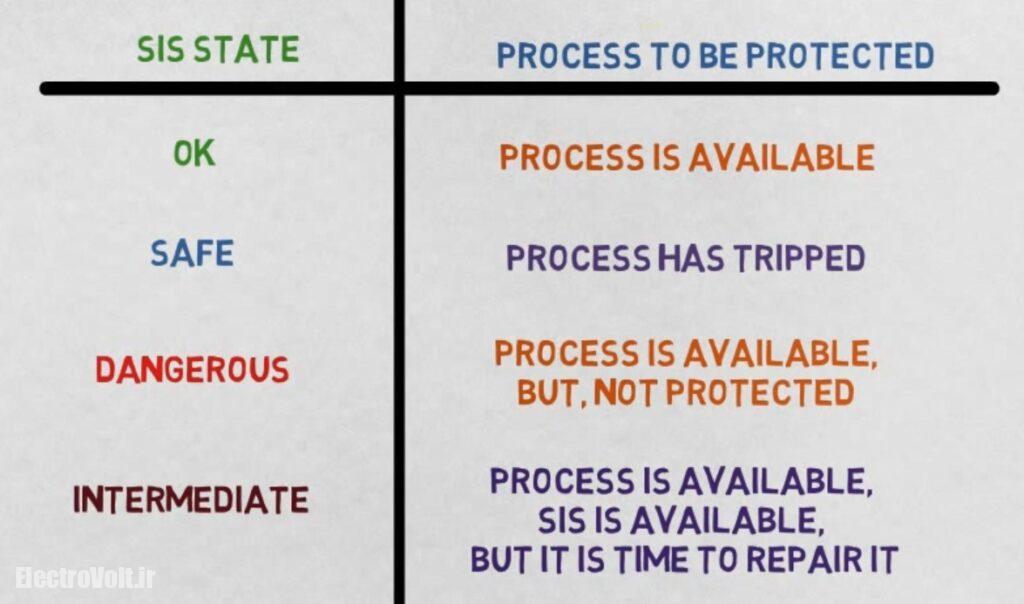
خطاهای SIS
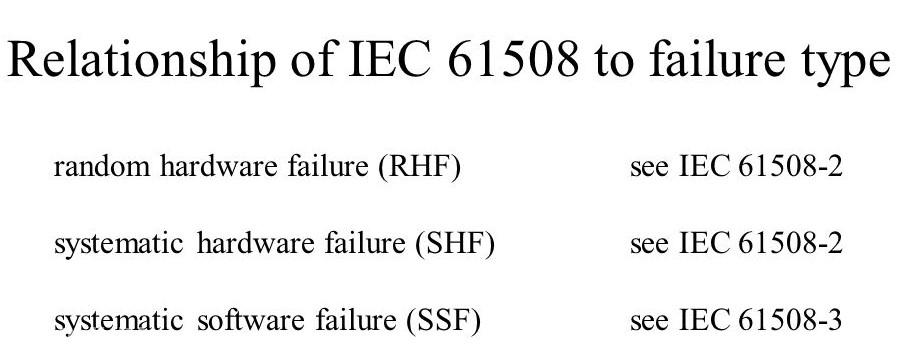
خطای سخت افزاری رندوم ( RHF ) : این خطا خود به خود اتفاق می افتد و کسی از زمان وقوع آن اطلاعی ندارد. برای مثال سوختن کنتاکت یک رله یا گیر کردن یک شیر برقی در حالت باز/بسته
خطای سخت افزاری سیستماتیک ( SHF ) : خطاهایی که به علت در نظر نگرفتن ویژگی های سخت افزاری تجهیزات همزمان برای دو یا چند کانال بوجود می آید. برای مثال زمانی که دو سنسور دما در یک محیط یکسان به علت بالا رفتن دما همزمان دچار خطا می شوند. راه حل این خطا استفاده از سنسورهای متنوع از شرکت های مختلف با بازه های عملکردی متفاوت است.
خطای نرم افزاری سیستماتیک ( SSF ) : خطایی مخفی که در طراحی یا پیاده سازی سیستم در نظر گرفته نشده باشد و میتواند به شکل مشخص، قطعی و قابل پیش بینی رخ دهد و به صورت رندوم نیست.
ایمنی عملکرد (Functional Safety )
یک سیستم مجهز به ایمنی ( SIS ) صد در صد از نظر عملکردی ایمن است اگر تمامی خطاهای رندوم و سیستماتیک آن باعث اختلال در عملکرد و در نتیجه باعث ایجاد حوادث مرگ و میر و خسارت های جانی و مالی و یا از بین رفتن تجهیزات نگردد. سیستم صد در صد ایمن در عمل وجود ندارد اما میتوان تا جای ممکن به این هدف نزدیک شد. ایمنی عملکرد ( Functional Safety ) به کاهش خطر در شرایط بحرانی در یک سیستم ایمنی ( Safety System ) گفته می شود. بنابراین ابتدا خطرات بالقوه ای که میتواند منجر به آسیب شود شناسایی می شود و سپس اقداماتی در جهت جلوگیری از بروز حادثه یا کاهش تاثیر یک حادثه انجام می گیرد. همچنین هر سیستم کنترل مرتبط با ایمنی باید به درستی کار کند، در غیر این صورت باید به روشی قابل پیش بینی و ایمن از کار بیفتد. برای به حداقل رساندن ریسک، استاندارد IEC 61508 محدود ساختن پیچیدگی سیستم را تا حد امکان توصیه می نماید. بدین معنی که یک سیستم متشکل از چند جز محدود دارای قابلیت اطمینان بسیار بالاتری نسبت به سیستمی است که دارای اجزا فراوانی می باشد.
یک سیستم ایمنی باید حداقل سه مورد الزامات SIL را برآورده سازد:
- قابلیت سیستماتیک (SC)، که سطح اطمینان از نظر طراحی محصول است – چه برای سخت افزار و چه برای نرم افزار (در صورت وجود)
- محدودیت های معماری ، که بیانگر محدودیت هایی در معماری اجزا است و ممکن است قابلیت اطمینان آن را تحت تاثیر قرار دهد
- PFDavg یا PFH ، که احتمال خرابی های تصادفی خطرناک است ، چه بر اساس تقاضا یا دیماند(بعدا توضیح داده خواهد شد) و چه بر اساس تعداد ساعات کارکرد.
استانداردهای عملکرد ایمن
برای امن کردن یک SIS از نظر عملکردی دو استاندارد مهم وجود دارد.
استاندارد IEC 61508 که ایمنی عملکرد از نظر الکتریکی، الکترونیکی و برنامه نویسی را شامل می شود. کاربردهای این استاندارد به شرح زیر است:
تجهیزات الکترونیکی قابل برنامه ریزی یا PES ( مخفف Programmable Electronic System ) برای مثال ترانزمیتر های فشار قابل برنامه ریزی
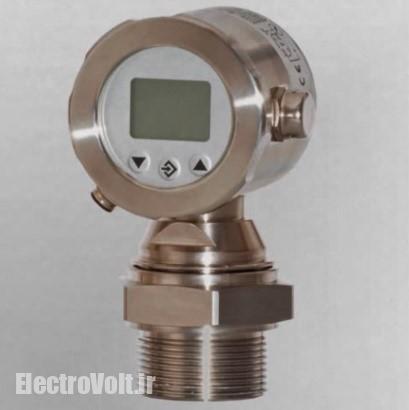
سیستم های خاموش کننده اضطراری یا ESD ( مخفف Emergency Shut Down )
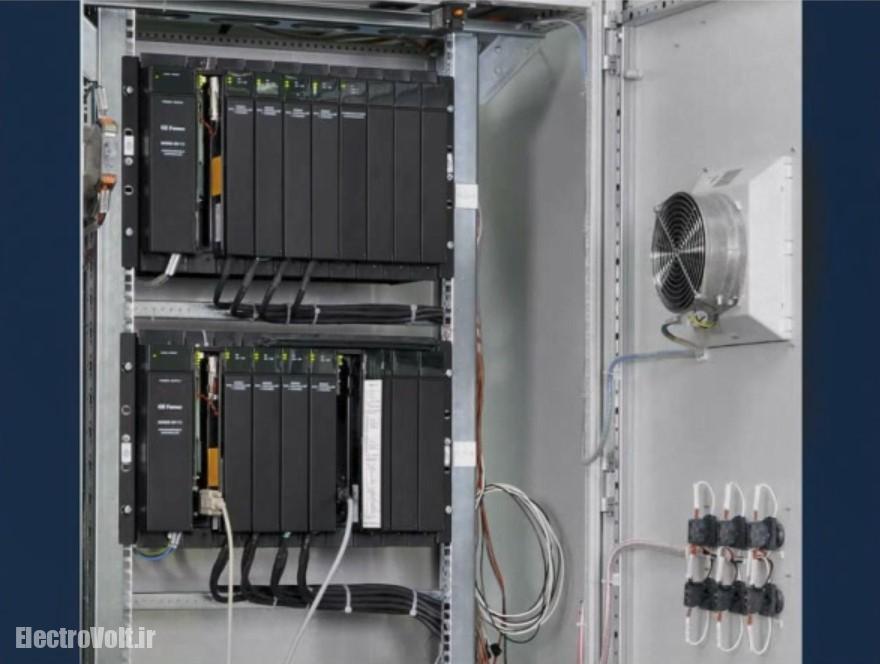
سیستم محافظتی فشار بالا یا HIPPS ( مخفف High Integrity Pressure Protection System ) که اکثرا به منظور محافظت از افزایش بیش از حد فشار در چاه های نفتی استفاده می شود.
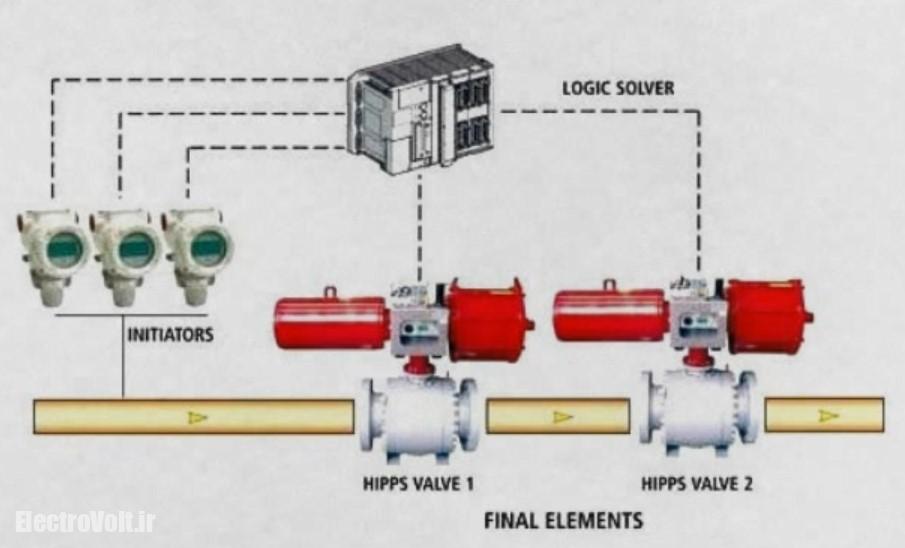
سیستم مدیریت سوخت شعله یا BMS ( مخفف Burner Management System ) که یکی از سیستم های حساس در مجتمع های نفتی به منظور گرم کردن آب و تولید بخار آب یا سوزاندن مواد شیمیایی زائد درون سیلندر زباله سوز استفاده می شود
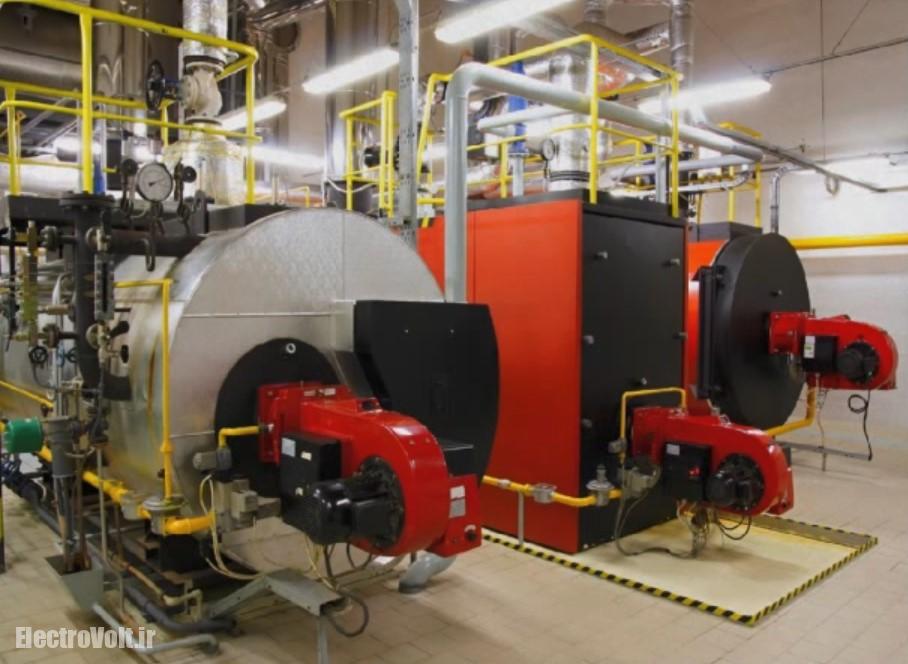
سیستم های F&G ( مخفف Fire And Gas ) که به منظور تشخیص نشت گاز، دود، شعله و تولید آلارم و فعالسازی سیستم های اطفای اتوماتیک حریق آبی، گازی و فومی استفاده می شود.
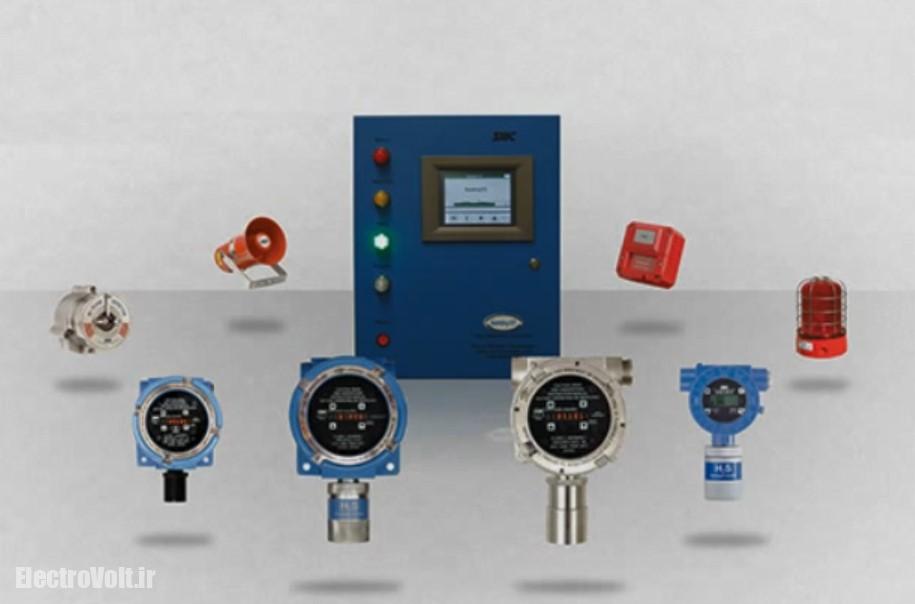
سیستم های ترمز اضطراری قطار یا EBS ( مخفف Emergency Break System )
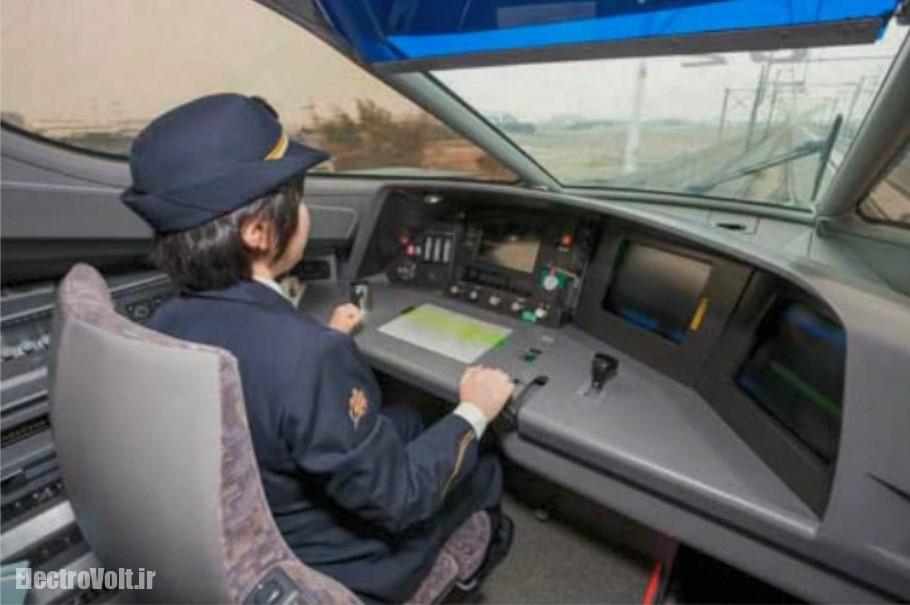
همچنین استاندارد IEC 61511 که از استاندارد IEC 61508 نشات گرفته شده است، به طور خاص برای SIS طراحی شده است. کاربردهای این استاندارد به شرح زیر است:
کلیه تجهیزات الکتریکی، الکترونیکی قابل برنامه ریزی
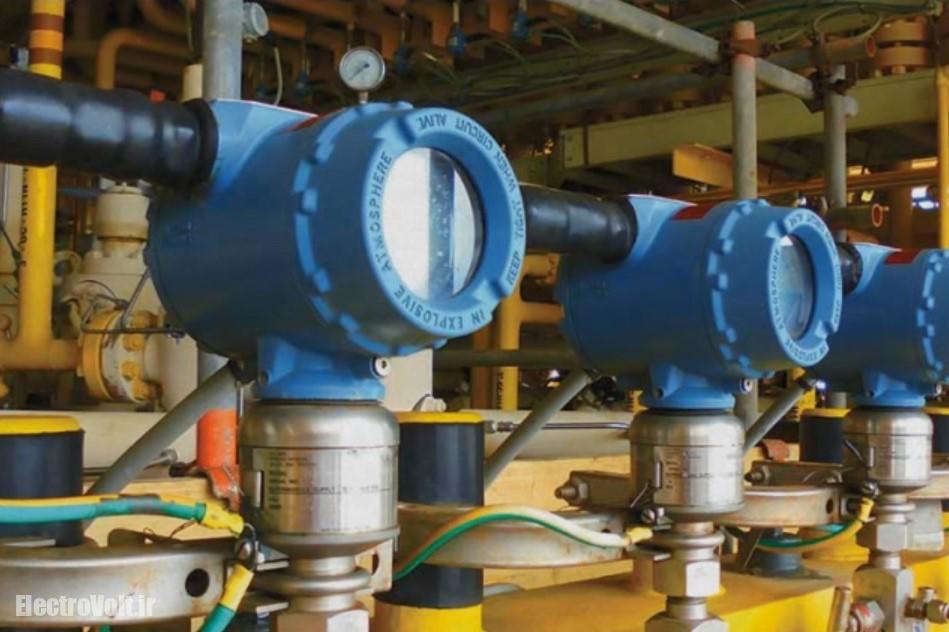
حل کننده های منطقی یا Logic Solver که به منظور تولید منطق مورد نیاز برای روشن کردن Actuator ها استفاده می شود
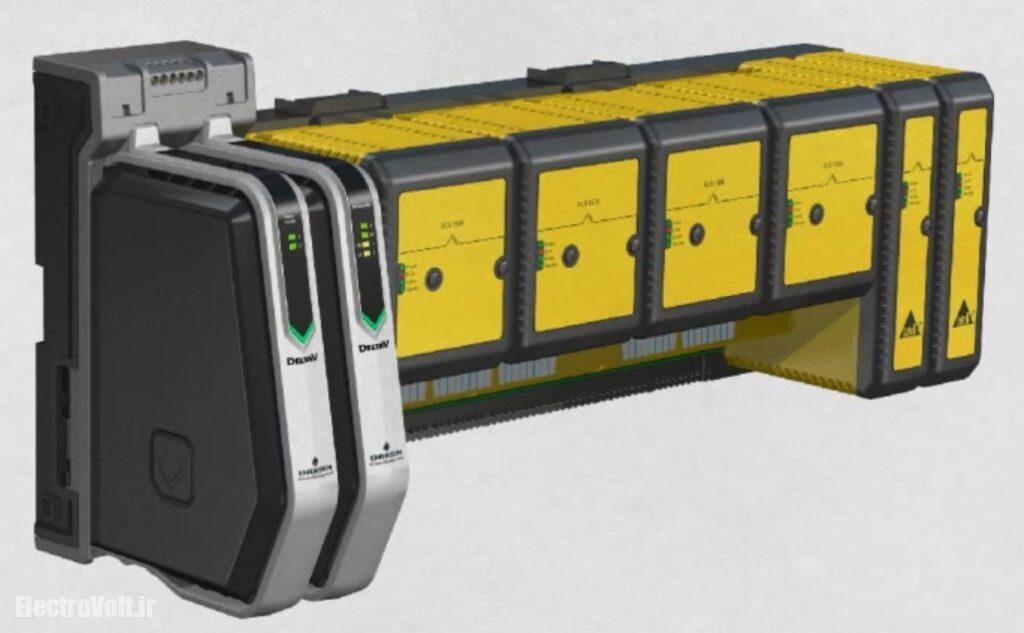
شیرهای برقی خاموش شونده در حالت اضطراری ( ESD Valve ) و شیرهای Blow Down
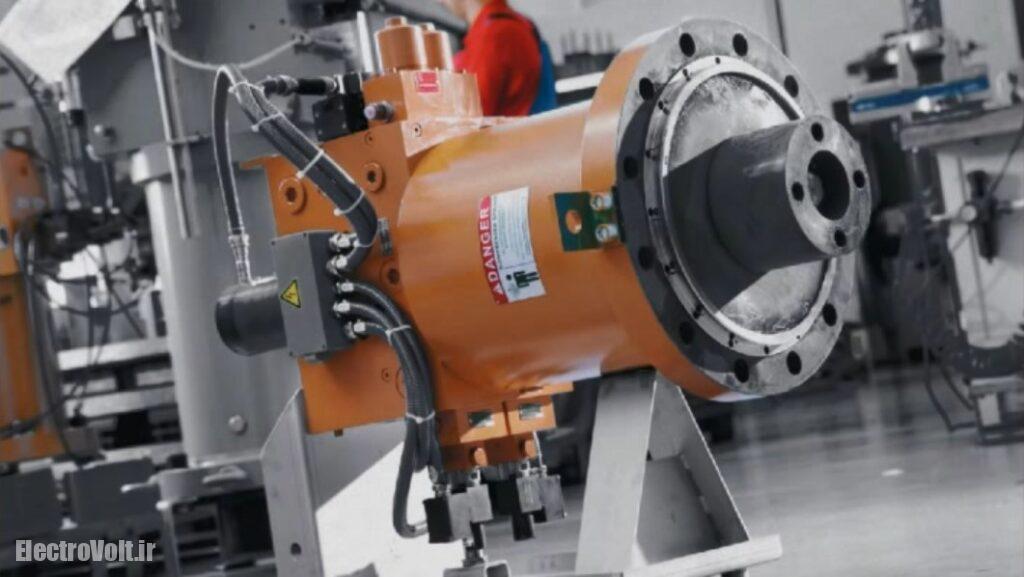
بنابراین اگر شما تولید کننده یا تامین کننده تجهیزات مربوط به ایمنی هستید لازم است از IEC 61508 پیروی کنید اما اگر شما طراح، برنامه نویس یا کاربر سیستم های SIS هستید نیاز است IEC 61511 را بدانید.
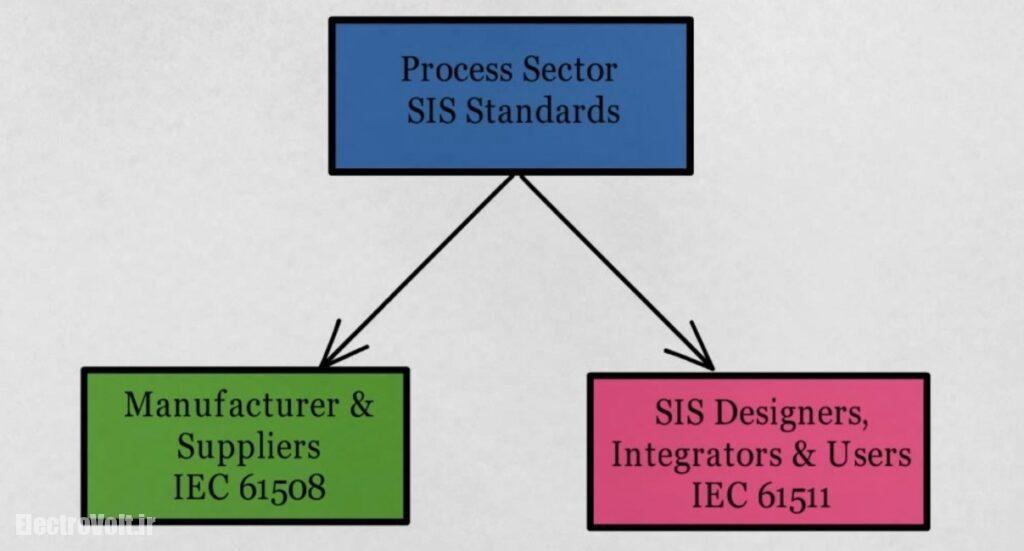
استاندارد IEC 61508
اولین ورژن از استاندارد بین المللی IEC 61508 توسط سازمان IEC در سال 1998 منتشر شد و در سال 2010 مورد بازبینی قرار گرفت. تاریخ احتمالی بازبینی بعدی 2024 می باشد. موضوع این استاندارد نحوه اعمال، طراحی، استقرار و نگهداری از سیستم های مرتبط با ایمنی است. این استاندارد در هفت بخش مختلف تدوین شده است. در بخش های 1 تا 3 الزامات استاندارد مشخص شده است. بخش 4 شامل تعاریف است. بخش های 5 تا 7 دستورالعمل ها و نمونه هایی برای توسعه و در نتیجه حاوی اطلاعات مفید هستند. استاندارد IEC 61508 اولین استاندارد بین المللی است که بکارگیری آن در تجهیزات الکتریکی، الکترونیکی و تجهیزات قابل برنامه ریزی الکترونیکی ( به اختصار E/E/PE ) به کاربرد آن تجهیزات بستگی ندارد. بنابراین استاندارد IEC 61508 یک استاندارد عمومی در مورد ایمنی عملکرد سیستم قابل استفاده در تمامی صنایع می باشد. اما استانداردهای دیگری زیر مجموعه این استاندارد وجود دارند که مختص صنایع و کاربردهای خاص هستند که در شکل زیر به برخی از استانداردهای زیر مجموعه IEC 61508 اشاره شده است.
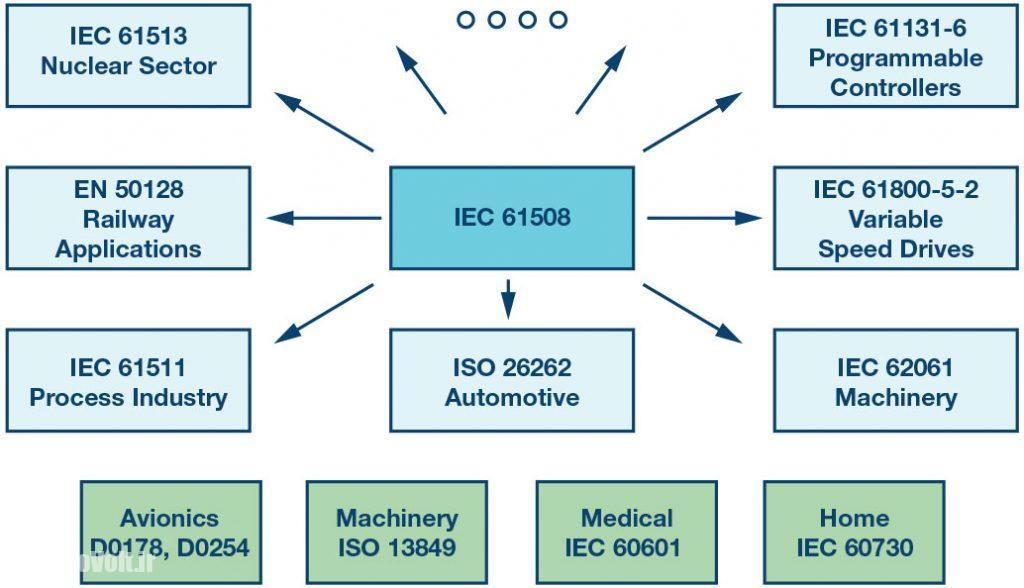
دلایل حوادث
طبق تحقیق سازمان TNO هلند که یک سازمان تحقیقاتی مستقل است 39.5 درصد از مجموع حوادث به علت خطای انسانی رخ می دهد که اکثر آن به خاطر ضعف در آموزش مناسب دادن به پرسنل، پایین بودن سطح دانش و یا عدم شایستگی نیروی انسانی می باشد. همچنین 34.5 درصد از مجموع حوادث به علت خطاهای رندوم غیر قابل کنترل نظیر کاهش توان منبع تغذیه، اتصال کوتاه و ضعف در طراحی می باشد. در حدود 26 درصد از حوادث هم به علت خطای تجهیزات کنترلی می باشد. برای مثال یک شیر برقی که گیر کرده باشد و نتواند به موقع عمل کند یا یک سنسور که اطلاعات صحیح دریافت نکند.
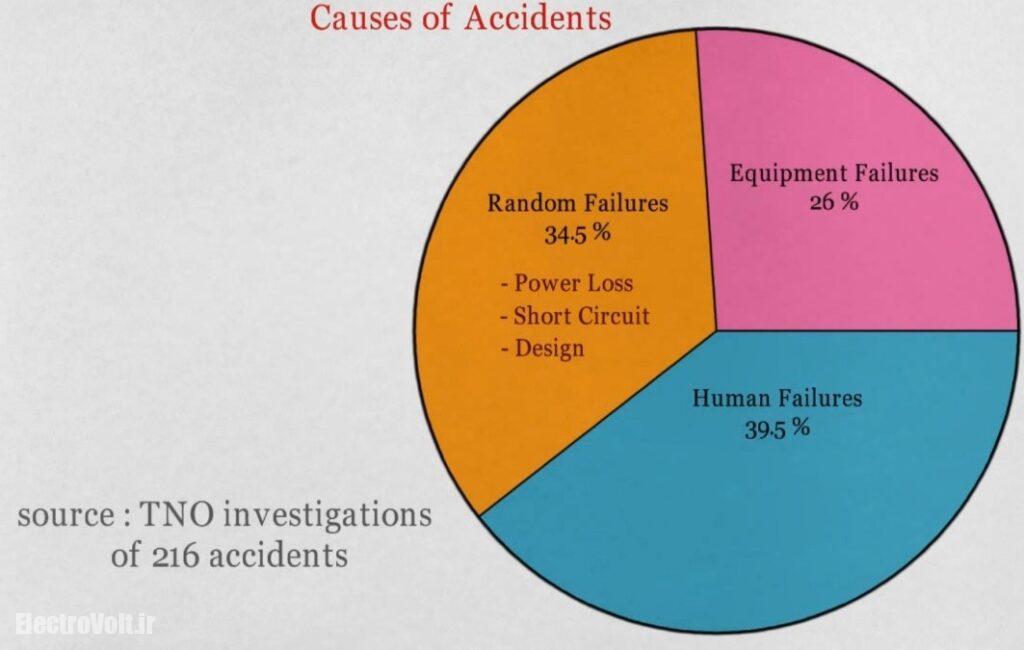
مدیریت عملکرد ایمن
ایمنی عملکرد به سه دلیل زیر نیاز به مدیریت دارد
- ایمنی بایستی تنها نتیجه یک پروژه می باشد
- ایمنی نباید به دست خوش شانسی سپرده شود و باید درباره نتایج اطمینان داشت
- ایمنی بایستی قابل رهگیری و قابل تکرار باشد
مدیریت عملکرد ایمن بر عهده تمام مجموعه های است که در چرخه حیاط ایمنی قرار دارند و بایستی نسبت به آن مسئولیت پذیری داشته باشند. خواه شخص باشد یا یک دپارتمان یا یک سازمان
به منظور مدیریت عملکرد ایمن بایستی داکیومنت دردسترس، مناسب، دقیق و قابل فهم وجود داشته باشد که شامل موارد زیر باشد :
- نحوه انجام دادن ایمنی
- تایید کردن ایمنی
- ارزیابی کردن ایمنی
- محاسبه کردن ایمنی
به طور معمول یک داکیومنت مدیریت عملکرد ایمن در هر فاز شامل اطلاعات زیر است :
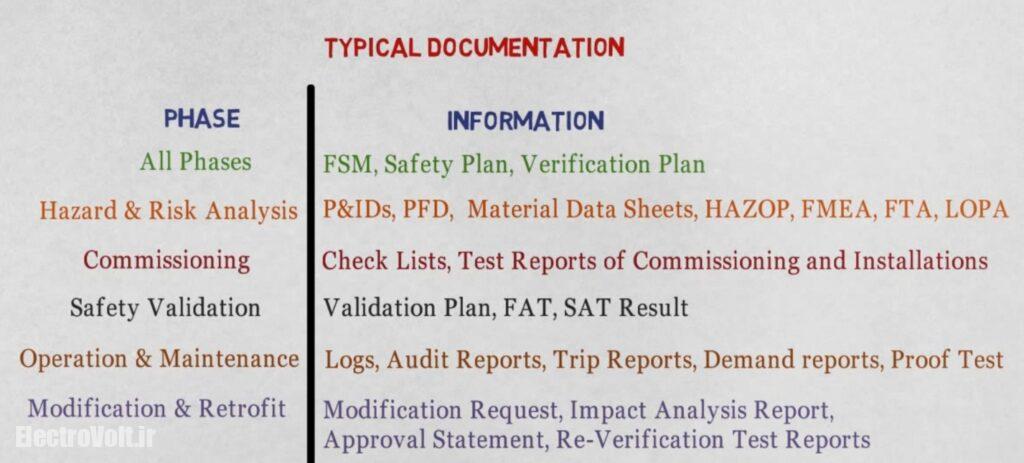
تغییر ( Modification )
منظور از تغییر هر گونه تغییری است که بعد از کامل شدن چرخه حیاط در سیستم ایمنی صورت می گیرد. فازهای چرخه حیاط می تواند طراحی، راه اندازی، تعمیرنگهداری و … باشد. منظور از کامل شدن یک فاز این است که تمام کارهای آن فاز به طور کامل انجام، تایید و اعتبارسنجی شده باشد.
به منظور ایجاد هرگونه تغییر نباید فقط شروع به تغییر کرد بلکه بایستی پروسه تغییر مناسب که توسط تیم تغییر تایید شده باشد را دنبال کرد. بنابراین تنها پرسنل واجد شرایط و آموزش دیده می توانند تغییر ایجاد کنند. برای اجرای این تغییرات بایستی درخواست رسمی داده شود سپس قبل از پیاده سازی هرگونه تغییری بایستی تاثیرات آن بر روی سیستم به طور کامل تحلیل شود و تصمیم گیری مبنی بر تایید شدن یا نشدن آن تغییر انجام شود.
تحلیل تاثیرات ( Impact Analysis )
منظور از تحلیل تاثیرات یک ارزیابی کامل از چگونگی تاثیر تغییر بر روی سیستم می باشد. برای فهمیدن اینکه آن تغییر چه تاثیری می تواند روی سیستم بگذارد تحلیل ریسک و خطا مجددا اجرا می شود. همچنین بایستی تضمین شود که تمام عملکردهای ایمنی در تمام زمان های اجرا شدن سیستم به درستی اجرا می شود. میزان شایستگی پرسنلی که میتوانند تغییرات را تحلیل کنند بر اساس میزان دانش و آموزش و تجربه آن ها مشخص می شود و بایستی به صورت دوره ای این میزان شایستگی چک و بروزرسانی شود.
تایید ( Verification ) و اعتبارسنجی ( Validation )
هر دو عبارت تایید و اعتبارسنجی زمانی که چیزی تست می شود معنی می دهد اما این دو یک چیز نیستند و با هم تفاوت دارند. تفاوت این دو به شرح زیر است :
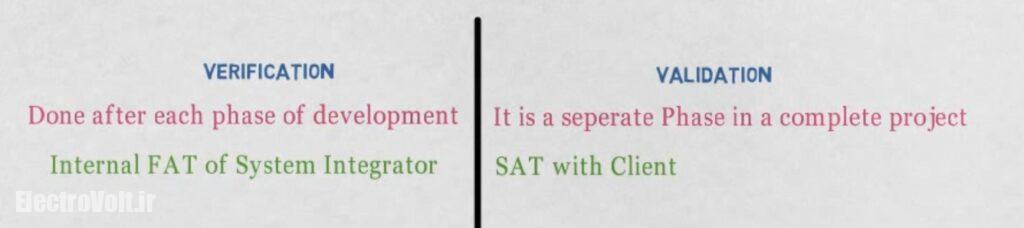
تایید کردن بعد از هر فاز از توسعه صورت می گیرد. برای مثال بعد از طراحی سیستم اما در عوض اعتبارسنجی به خودی خود یک فاز جداگانه از یک پروژه کامل محسوب می شود.
تایید کردن به صورت FAT ( مخفف Factory Acceptance Test ) به معنای تست کارخانه ای قابل پذیرش، به صورت درونی به منظور یکپارچه سازی سیستم صورت می گیرد در حالی که اعتبار سنجی با سخت افزار و نرم افزار واقعی به صورت SAT ( مخفف Site Acceptance Test ) توسط سرویس گیرنده ( Client ) در سایت اجرا می شود.
یک مثال برای تایید و اعتبار سنجی در هنگام انتخاب وسیله صحیح برای یک لوپ SIL2 :
مهندسین تایید می کنند برای هر تجهیز، پارامترهایی نظیر SFF ( مخفف Safe Failure Fraction ) به معنای ضریب شکست ایمنی و HFT ( مخفف Hardware Fault Tolerance ) به معنای تلورانس خطای سخت افزار و همچنین شرایط محیطی و … مناسب لوپ SIL2 است.
مهندسین عملکرد ایمنی تجهیز را برای فهمیدن اینکه آیا واقعا SIL2 است یا خیر با اجرای تست SAT اعتبار سنجی می کنند.
ارزیابی عملکرد ایمنی ( Functional Safety Assessment )
ارزیابی عملکرد ایمنی یا FSA چک کردن این است که همه چیز بر طبق طراحی انجام شده باشد. FSA برای هر فاز بایستی انجام می گیرد. برای مثال ارزیابی بعد از فاز راه اندازی
نکته حائز اهمیت FSA این است که ارزیابی بایستی با توجه به ایمنی مورد نیاز دارای درجه کافی از استقلال باشد. منظور از استقلال این است که اگر یک لوپ دارای SIL1 یا SIL2 باشد یک شخص مستقل به اندازه کافی برای اجرای ارزیابی مناسب است اما اگر لوپ دارای SIL2 یا SIL3 باشد بایستی یک دپارتمان مستقل جداگانه عملکرد ایمنی را ارزیابی کنند. برای ارزیابی عملکرد ایمنی لوپ های SIL3 و SIL4 بایستی دو سازمان مستقل جداگانه استخدام شود. جدول زیر این موضوع را لیست کرده است.
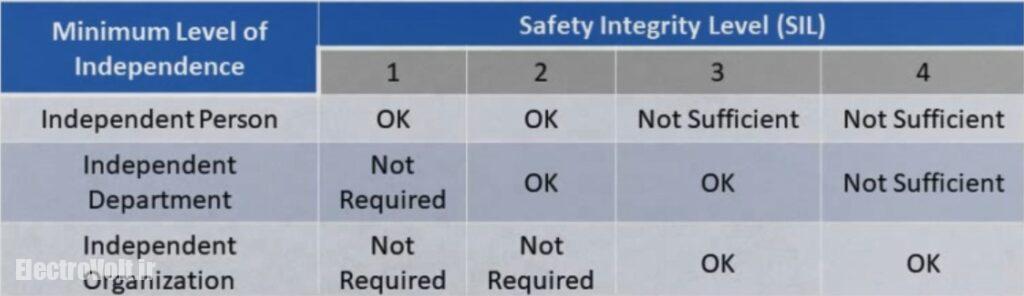
بازرسی ایمنی ( Safety Audits )
بازرسی ایمنی شبیه به FSA است. در واقع به اجرای ارزیابی عملکرد ایمنی که به صورت دوره ای و در فازهای طولانی تری نظیر تعمیر و نگهداری انجام شود بازرسی ایمنی گفته می شود. بازرسی می تواند به صورت سالانه، شش ماهه، ماهیانه و یا در تعمیرات اساسی ( Overhaul ) انجام شود. همان قوانین در خصوص مستقل بودن بایستی در بازرسی نیز رعایت شود.
تحلیل خطر و ریسک
نامگذاری های مختلفی برای تحلیل خطر وجود دارد که در شکل زیر مشاهده می کنید:
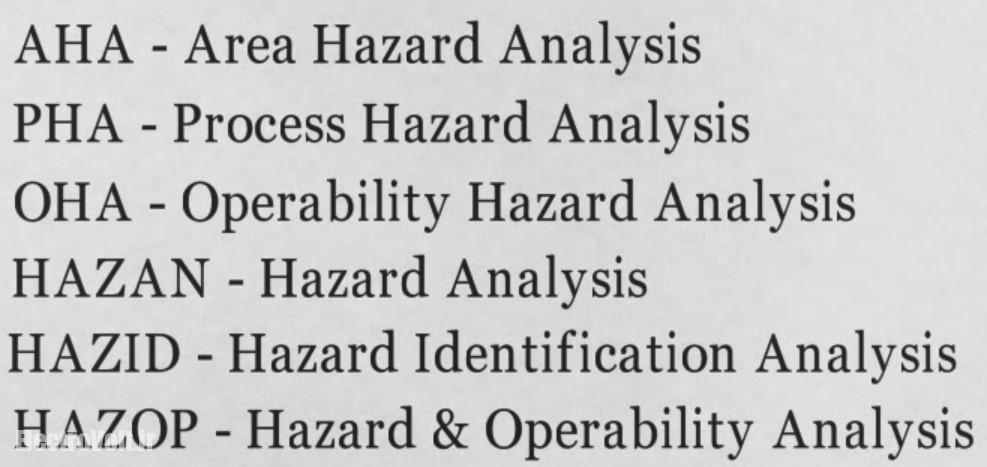
از میان این نامگذاری ها تحلیل خطر HAZOP بیشترین کاربرد را دارد.
خطر ( Hazard ) چیست ؟
بر طبق استانداردهای IEC 61508 و IEC 61511 خطر به منبع پتانسیل بالقوه خسارت ( Source Of Harm ) گفته می شود.
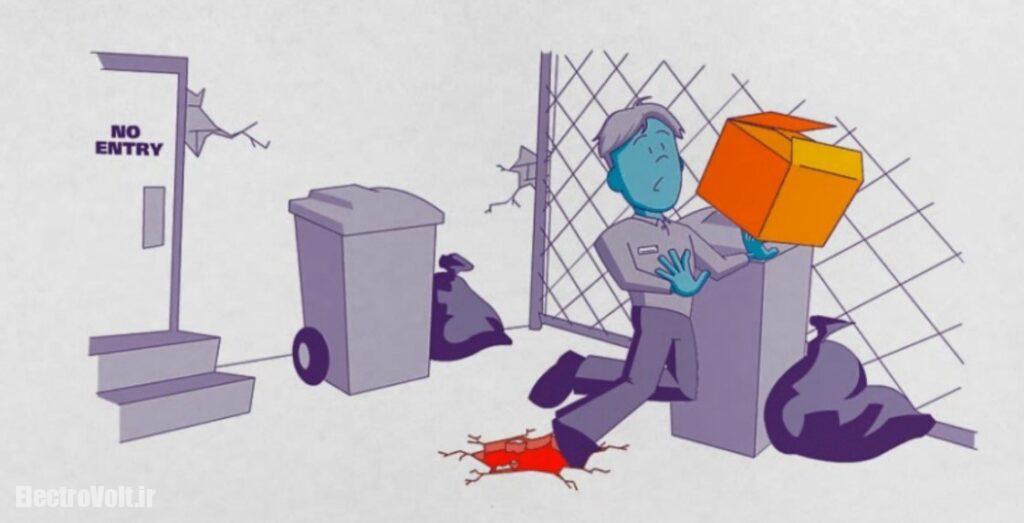
رخداد خطرناک ( Hazardous Event ) چیست ؟
رخداد خطرناک زمانی اتفاق می افتد که پتانسیل بالقوه خطر بالفعل شود و حادثه اتفاق بیوفتد. پس برای اینکه هازارد آسیب برساند بایستی رخداد خطرناک اتفاق بیوفتد. به احتمال تبدیل شدن خطر بالقوه به بالفعل احتمال خطر گویند.
برای مثال به سیلندر بزرگ شکل زیر توجه کنید که برای کمک به پرسنل و ماشین آلات بر پا شده است.
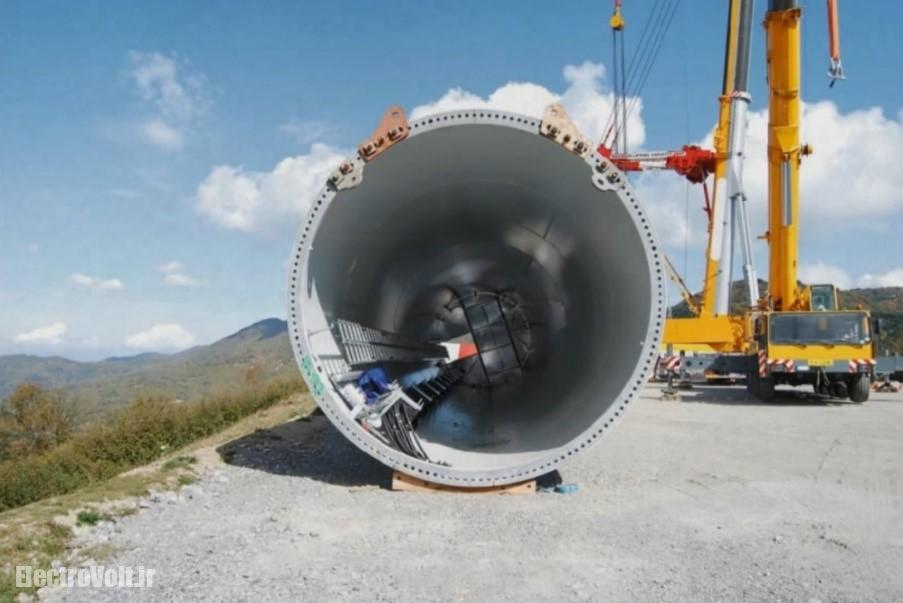
- شناسایی خطر ( Hazard Identification ) : اگر کابل نگهدارنده سیلندر به خودی خود یا توسط خطای انسانی پاره شود، می تواند در دو جهت حرکت کند. یا از صخره به پایین پرتاب شود یا به سمت پرسنل حرکت کند. عواقب چنین حادثه ای خسارت به خود تجهیز یا پرسنل اطراف آن می باشد. بنابراین ما در مرحله اول دو هازارد را شناسایی کردیم.
- تحلیل خطر ( Hazard Analysis ) : فرض کنید احتمال اینکه این سیلندر به پایین پرتاب شود یک بار از هر 100 بار و احتمال اینکه به سمت پرسنل حرکت کند 1 بار از هر 100 بار باشد. بنابراین احتمال آسیب دیدن شخصی 1 از 10.000 می باشد.
- کاهش ریسک : یکی از راه های کاهش ریسک استفاده از ویجت برای کاهش حرکت سیلندر به سمت راست/چپ و همچنین استفاده از چندین کابل نگهدارنده به جای استفاده از یکی می باشد.
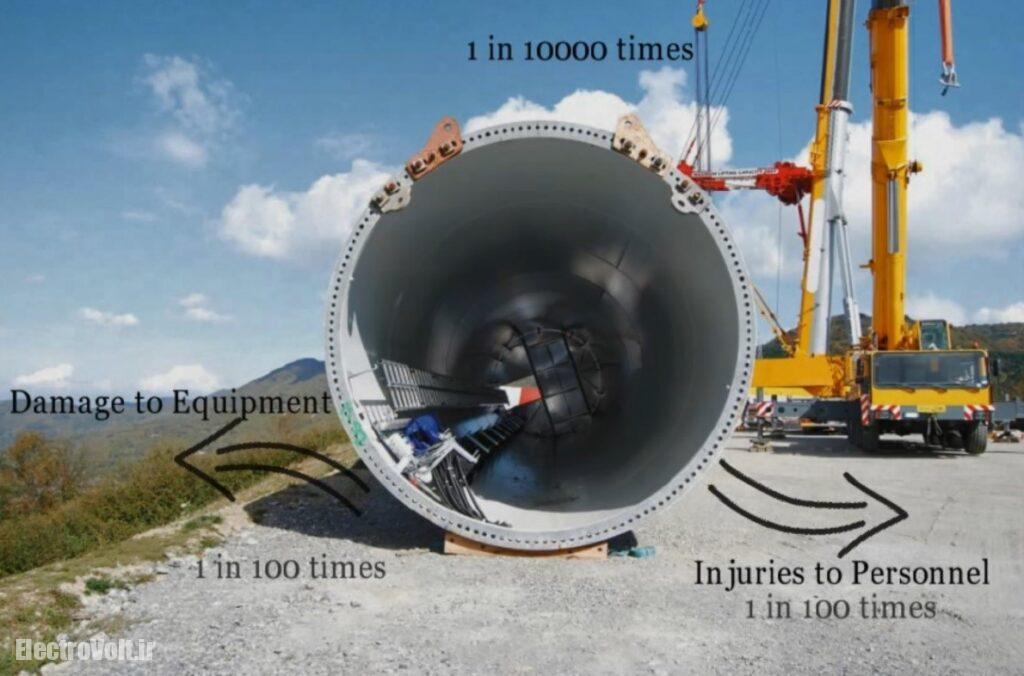
ما در این مثال خطرات را شناسایی و بر اساس دانش و دیتای قبلی تحلیل کردیم. سپس بر اساس اعمال مناسب ریسک را کاهش دادیم. زمانی که تمامی خطرات بالقوه شناسایی شود نیمی از کار انجام شده است. شناسایی خطرات اولین و مهمترین گام برای شناسایی عملکرد ایمن مورد نیاز برای SIS می باشد. به خاطر داشته باشید که اگر یک عملکرد ایمن به خطر یا رخداد خطرناک متصل نباشد بلا استفاده است. از مرسوم ترین تکنیک های شناسایی خطرات تحلیل چک لیست، تحلیل چه می شود اگر، حالت خطا، تحلیل اثر، تحلیل درختی خطا و HAZOP می باشد که در اینجا ما به دو مورد آخر یعنی تحلیل درختی خطا و HAZOP اشاره خواهیم کرد.
ریسک چیست ؟
ریسک حاصل ضرب شدت عواقب ( Consequences ) در فرکانس وقوع آن عواقب می باشد. برای مثال یکی از عواقب می تواند مرگ یک نفر باشد و وقوع آن می تواند یک بار در هر سال باشد.
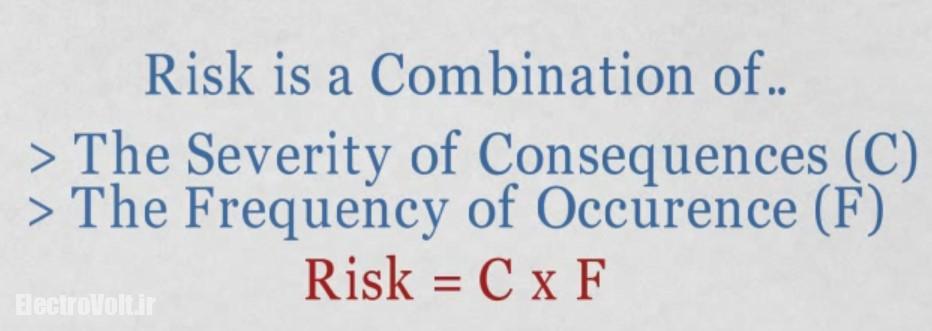
همواره نیاز داریم که ریسک مرتبط با رخدادهای خطرناک را محاسبه کنیم و تعیین کنیم که از ریسک قابل قبول ما کمتر باشد. اگر ریسک با رخداد خطرناکی همراه نباشد نمی توان مقدار آن را مشخص کرد. معمولا دولت ها و قوانین دولتی مقدار ریسک قابل تحمل را مشخص می کنند. برای مثال در UK مقدار حداکثر ریسک قابل تحمل عمومی 10-4 می باشد که در مقایسه با آلمان بزرگتر است. در آلمان ریسک قابل تحملی وجود ندارد.
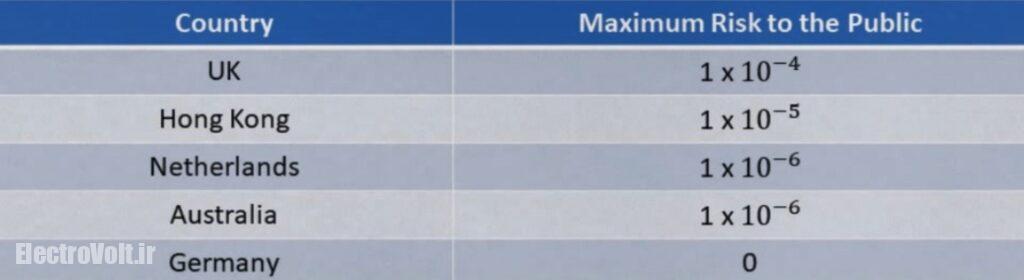
کاهش ریسک
جایی که دقیقا حادثه اتفاق می افتد در محدوده وقوع رخداد خطرناک می باشد. ریسک در این ناحیه بالاترین حد خود است. برای کاهش ریسک از تکنیک های کاهش ریسک بایستی استفاده شود تا ریسک تا اندازه ریسک قابل قبول ( tolerable risk ) کاهش یابد. همچنین می توانیم با استفاده از لایه های محافظتی ریسک رخداد خطرناک را به حداقل برسانیم. برای مثال شکل زیر را در نظر بگیرید که در آن ریسک را با استفاده از SIS1 ، SIS2 ، TANK DIKE و BURSTE PLATE تا اندازه قابل قبول کاهش دادیم.
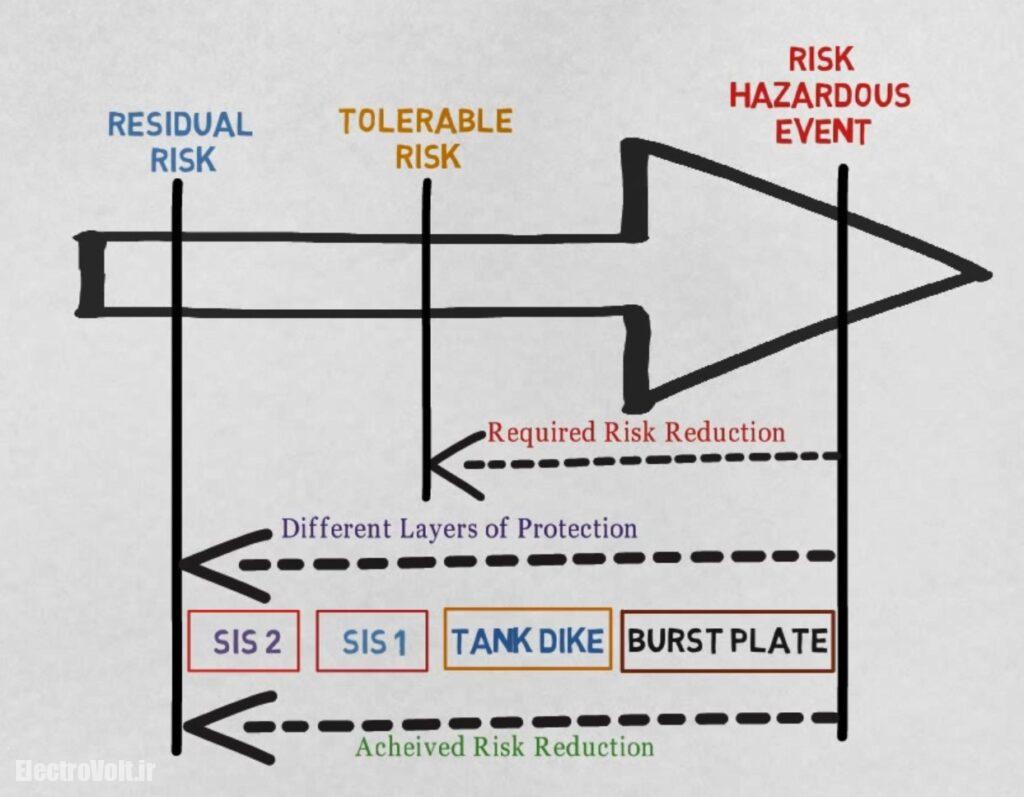
سرفصل های بعدی آموزش SIL :
تحلیل عملیاتی خطر ( HAZOP )
تحلیل لایه های محافظتی ( LOPA )
تحلیل حالت شکست و اثر ( FMEA )
تحلیل درختی خطا ( FTA )
تحلیل درختی رخدادها ( ETA )
نکات طراحی سخت افزار ایمن
نکات طراحی نرم افزار ایمن
نحوه محاسبه تلورانس خطای سخت افزاری ( HFT )
نحوه محاسبه کسر شکست ایمنی ( SFF )
بلوک دیاگرام قابلیت اطمینان ( RBD )
تحلیل مارکوف ( MA )
برای دریافت کل مطالب فوق به لینک زیر مراجعه کنید :
1 دیدگاه
سلام و درود
تشکر میکنم بابت مطالب فوق العاده کاربری که ارائه دادین.